Material Requirement Planning (MRP) in ERP Software
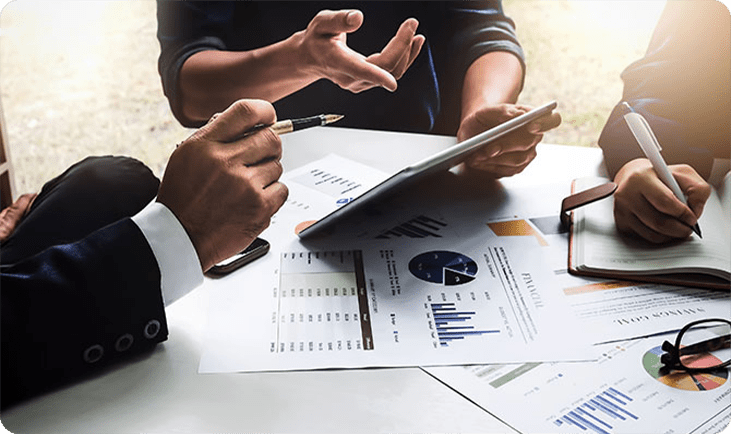
MRP SYSTEM MEETS YOUR CUSTOMER COMMITMENTS WITH IMPROVED PLANNING

Production planning software, commonly known as Material Requirements Planning (MRP) in ERP optimizes your procurement of raw materials, allowing you to maintain optimum inventory levels while minimizing carrying costs. MRP gives planners a detailed, consolidated view of supply and demand. Once a production plan is firmed up, MRP can be used to create purchase orders based upon demand from firm planned MPS orders, open production batches, sales orders and forecasts.
Planners have a calendar view of planned orders with drill down, analysis, grouping and rescheduling capabilities. Through planning dashboards, planners can create a relation between demand and supply and determine why and when an item is required.
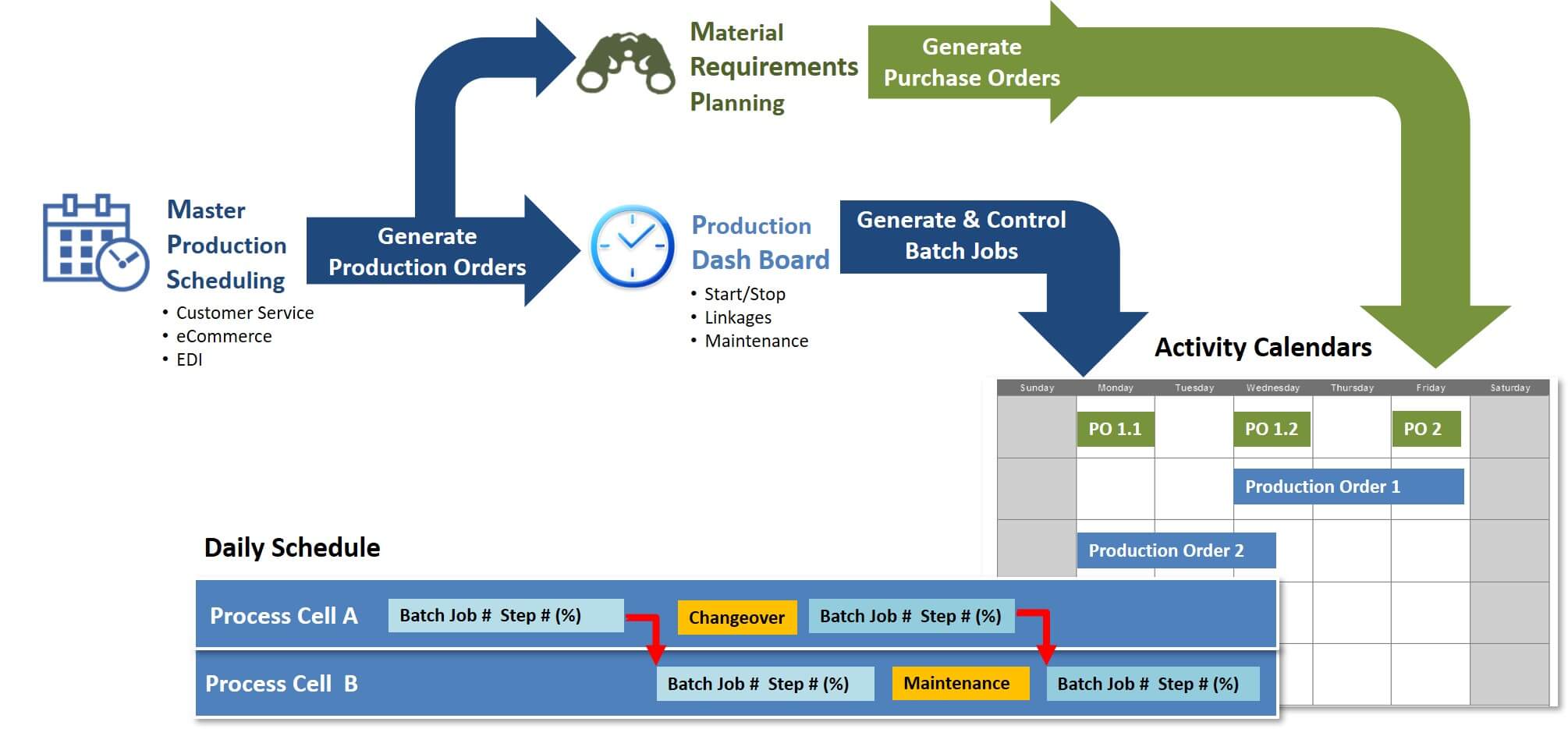
MATERIAL REQUIREMENTS PLANNING SOFTWARE THAT WILL CHANGE THE WAY YOU WORK

MRP ERP software creates the optimal number of purchase orders required to meet current and forecasted production jobs, so that you can meet your customer service promises, in terms of perfect orders and delivery dates.
- Easily create purchase orders based on demand
- Employ the Visual Workbench to view procurement orders by item, warehouse, and vendor
- Extensive reporting, including expedite reports, to manage the entire procurement function
- Schedule Intermediate batches required to meet MPS production
- Run MRP by Warehouse, or by an item or a range of items across warehouses
MASTER PRODUCTION SCHEDULING

Master Production Scheduling (MPS) provides a master plan for what you need to produce, how much and when to produce it. Your open production orders, sales orders and forecast entries are used as finished goods demand, and your inventory levels, batch production jobs, and receipts are considered as supply.
NEED AN ADVANCED PRODUCTION SCHEDULING TOOL?

Take advantage of a finite capacity scheduling tool that creates and adjusts production schedules in minutes and considers:
- Available labor force, including their calendars and their skill sets.
- The cost to produce an item on a piece of equipment.
- Inventory shortages at the time of batch job production.
- Incremental batch job tasks, including equipment setups.
- Machine availability, sequencing rules and other secondary constraints.
CONTACT US / REQUEST A DEMO
