Process manufacturing refers to transforming raw materials into finished goods using a calculative formula or recipe. The process involves multiple stages, from planning and procurement to production, quality control, packaging, storage, and distribution.
Process manufacturing is used in industries where items are produced in bulk. These industries include:
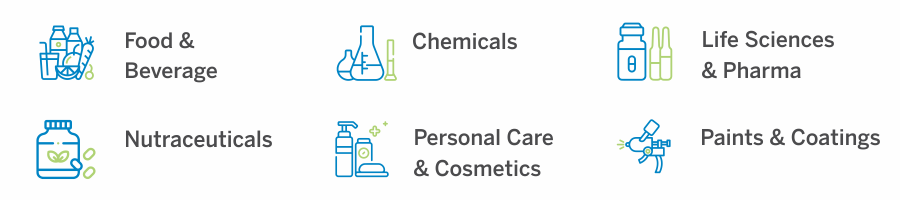
Process manufacturing includes blending, mixing, and having irreversible chemical reactions. For example, when mixed, you cannot separate chemicals (raw materials) from the finished goods.
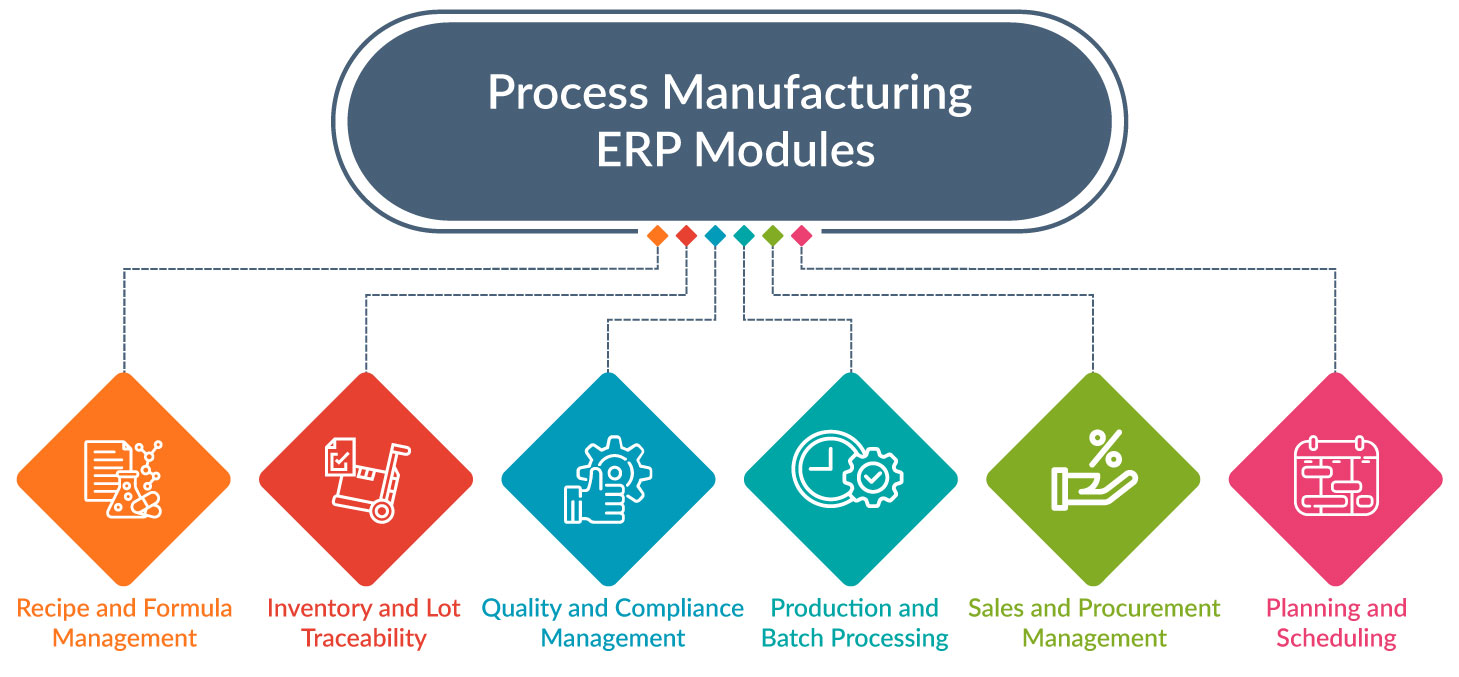
Importance of ERP in Streamlining Operations and Accelerating Performance
Enterprise Resource Planning (ERP) is business management software that helps businesses streamline operations, improve efficiency, and ensure compliance. It provides a unified view of activity for a single source of truth. An ERP system consists of integrated business modules that share a common database, which means all your business data is on a single platform. Let’s look at the critical ERP modules that manufacturers seek and their roles.
1. Recipe and Formula Management
Recipe and formula management is critical in process manufacturing. ERP allows manufacturers to define product ingredients, manage product specifications, embed QC tests, manage multiple formula versions, and more. Let’s see how process manufacturing ERP can help you manage things:
- Define fixed and variable labor costs, including consumable costs
- Employ workflow approval processes
- Leverage actual inventory costs within packaging specs
- Dynamically adjust ingredients to meet target characteristics
- Reduce time spent on tedious, error-prone manual calculations to develop, analyze, and approve formulas
2. Inventory and Lot Traceability
Inventory management and lot traceability help manufacturers track items throughout the supply chain (from purchase and production to delivery). This module tracks the movement, usage, and location of inventory items with the help of batch or lot numbers. Inventory records are tracked in terms of their QC statuses, volumes, weights, plant location, and licenses. Inventory management and lot traceability functionality allow process manufacturers to:
- Auto generate lot numbers for intermediate and finished goods
- Link dependent batches together
- Assign equipment and labor resources to batch jobs
- Track forward traceability from raw materials to finished goods, as well as raw material suppliers
- Track backward traceability, from customer complaints to finished goods and raw materials
- Prioritize and expedite batch jobs
3. Quality and Compliance Management
Quality management and compliance modules in process manufacturing ensure that the products meet industry standards, customer expectations, and regulatory compliance. Process manufacturing industries include pharma, chemicals, food and beverage, cosmetics, and more, where product consistency and safety are paramount.
ERP solutions ensure that inventory items and finished products meet strict quality standards while avoiding fines and penalties. Lot management and transactional audit reporting help you meet regulatory compliance mandates.
- Quality and Compliance Management supports food-related labeling: GMP, FDA, and GFSA requirements
- Run graphical bidirectional lot traceability inquiries
- Support labels such as GMP, SARA Type III, REACH, HAZMAT, SDS, MSDS, and INCI requirements for the chemical industry
- Embed QC tests and Standard Operating Procedures (SOP) within formula specifications
4. Production and Batch Processing
Process manufacturing manages mixing, blending, filling, assembling, and other manufacturing processes to produce finished goods and intermediaries. It supports make-to-stock operations, custom blenders, private labels, and more. With a dedicated module for batch processing and production management, manufacturers can calculate precise ingredient quantities for consistent batch manufacturing.
- Scheduling and managing batch-wise production
- Work-in-progress (WIP) tracking and yield management
- Optimizes machine and labor efficiency
5. Sales and Procurement Management
Also known as the purchase module, this module automates the procurement process in the manufacturing sector, from identification to payment. It streamlines tasks, generates purchase orders, manages invoices, tracks deliveries, and analyzes spending patterns. This module simplifies complex order-to-pay cycles, including creating invoices, payments, and receipts.
The sales module in ERP software helps create quotes, enter orders, and manage invoices, while spotting trends, behaviors and sales opportunities. It allows manufacturers to:
- Record sales activities
- Manage opportunity analysis
- Create and check sales quotation
- Manage orders and delivery
- Create dynamic reports
Process manufacturing ERP software can help your business flourish while automating operations
6. Planning and Scheduling
Master Production Schedule provides a master plan for production. It helps you plan for the items needed for manufacture, the amounts needed, and when to produce them.
Production scheduling software, commonly known as Master Production Scheduling (MPS) in ERP, provides a master plan for what you need to produce and how much and when to make it. Your open production orders, sales orders, and forecast entries are used as finished goods demand, and your inventory levels, batch production jobs, and receipts are considered supply. MPS generates an accurate, detailed schedule of orders across one or more plants based upon this granular view of supply and demand.
- Ensuring timely procurement of raw materials
- Managing supplier relationships and purchase orders
- ERP’s role in demand forecasting and cost reduction
Material Requirements Planning (MRP) functionality allows manufacturers to maintain optimum inventory levels while helping create purchase orders based on demand from planned MPS orders, open production batches, sales orders, and forecasts.
With MRP, manufacturers can:
- Employ the Visual Workbench to view purchase orders by item, warehouse, and vendor
- Schedule intermediate batches required to meet MPS production
- Create reports, including expedited reports, to manage the entire procurement function
- Run MRP by warehouse or by item
Learn how BatchMaster, a leading process manufacturing ERP process manufacturing ERP , can help your manufacturing business with version control, label claims, document and label generation, and traceability and recall functionality.
Benefits of Process Manufacturing ERP Modules
Each module offers a range of benefits, including:
1. Real-Time Data Visibility
The right ERP module saves costs by enabling real-time data input. Instead of manually coordinating and assigning resources and projects, you can use role-based dashboards for each process, effectively managing and centralizing data. This eliminates the need for searching, creating, and updating business data on paper and spreadsheets. As a result, targeted prioritization becomes possible, boosting efficiency and productivity in all aspects of operations.
2. Scalable Batch Manufacturing
Process manufacturing ERPs include recipe or formula management. This enables businesses to calculate precise ingredient quantities for consistent batch manufacturing. It effectively manages units of measurement and automatically adjusts volumes and amounts as required, reducing manual errors. This ensures that batches are consistently produced to high standards. It also allows seamless integration of changes in customer orders into production processes, securely storing relevant information.
3. Industry-Specific Compliance
Process manufacturers face strict regulatory requirements to ensure product quality and compliance. Industries such as food, chemicals, pharmaceuticals, nutraceuticals, and more must adhere to specific regulations governing ingredients and product safety. ERP systems simplify industry compliance by integrating compliance requirements into production workflows. They facilitate easy updates to data sheets and enable quality checks, ensuring that the team operates by the latest legislation. Comprehensive lot management capabilities enable you to perform product searches and recalls in minutes.
To Sum Up
The process manufacturing industry encompasses various sectors such as food and beverages, pharmaceuticals, nutraceuticals, and chemicals. These sectors have their own unique business models, trends, and challenges. Therefore, organizations should choose an ERP solution that provides modules catering to their specific industry sector and addresses their challenges effectively.
BatchMaster ERP software offers modules that streamline day-to-day operations, providing a centralized platform to store and access any data as per your requirements.
Contact our experts to learn about the must-have modules for your company that can significantly impact process optimization and productivity.