BatchMaster Web ERP (aka BME Web)
A Single, Unified ERP developed by BatchMaster Software
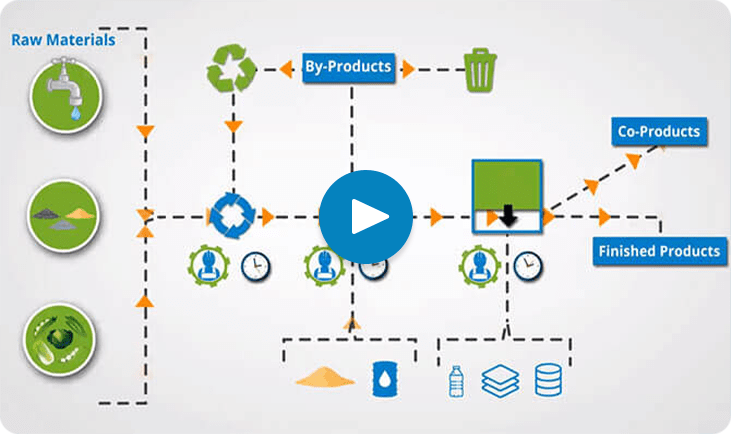
Introduction To BatchMaster Manufacturing Solutions
Introduction

Challenge:
Running our add-on manufacturing app, BatchMaster Manufacturing, with either QuickBooks or Sage 100/300, requires users to have a login credentials to both applications. Running these 2 integrated software applications can poise some challenges for some users in terms of data visibility and reporting across manufacturing and financials.
Solution:
BatchMaster Web ERP, aka BME Web, combines BatchMaster Manufacturing with BatchMaster’s own Finance modules, thus replacing the need for QuickBooks or Sage 100/300. A single user login to our unified ERP solution can manage and report on all aspects of your business.
As a natively web-built application, BME Web runs just with the URL, a web browser, internet-enabled device, and login credentials, offering you remote access to your business — from anywhere, anytime.
BatchMaster Web ERP Overview

BatchMaster Web ERP is a cost-effective ERP application developed by BatchMaster Software for process manufacturers in the food, chemicals, nutraceutical, and life sciences industries. Our ERP application manages Inventory, Sample Management, Lab, Formulation, Packaging, Planning, Scheduling, Production, Costing, Quality, Compliance, Warehousing, as well as the back-office functions for Accounting, Sales, Purchasing, and Distribution.
Equipped with an intuitive UI, which is user customizable, that offers real-time, accurate data visualizations and drill down reporting capabilities, plus in-context analytics across these essential modules:
Accounting
Sales
Purchasing
Key Modules & Features

A brief description of modular functions found in BatchMaster ERP Web is as follows:
Inventory Management
- Maintain and convert inventory across multiple units of measurement.
- Get a view of SKU inventory based upon weights, volumes, and count quantities.
- Manage lot-controlled inventory based upon variable inventory characteristics, including quality status, expiration dates, and strength or potency values.
- Manage inventory down to the license plate and bin level.
- Perform inventory movements and adjustments, such as cycle counts and physical inventories.
Planning & Scheduling
- Use time-phased inventory inquiries of raw materials and finished goods to generate purchases orders and batch jobs, respectively.
- Use advanced, automated MPS & MRP modules to generate purchases orders and batch jobs, respectively.
- Capable of handling both make-to-stock (forecast) and make-to-order (SO) demands.
- Direct transfer of orders to purchase and production.
- Ability to consolidation demand when creating batch jobs and PO’s
- Considers both purchase and QC lead time to ensure on-time delivery.
Batch Production
- Dynamically size batch jobs.
- Prioritize and expedite specific batch production jobs.
- Auto-create production order against sales orders.
- Report shortages of required ingredients and materials.
- Report shortages of required ingredients and materials.
- Manage single super batch job consisting of multiple linked batch jobs.
- Adjust batch formula prior to batch job release and during WIP.
- Auto generate lot numbers for intermediates and finished goods.
- Mandate execution of QC tests and manufacturing instructions.
- Auto back flush consumed ingredients and materials.
Quality Control & Quality Assurance
- Establish library of standardized QC tests and sample plans.
- Define QC tests for formulas, raw materials, intermediates, and finished goods.
- Ensure the sequential execution of QC tests.
- Auto assign lot statuses and disposition lots, based upon QC test results.
- Analyze QC tests results by item, lot, batch job and vendor.
- Auto-generation of non-conformance for failed QC tests with provision of CAPA.
Formulation
- Separation of formulas from finished goods packaging bills of material.
- Formula security with approval, status, and complete audit trail tracking.
- Formula version control with roll-back capability
- Embed QC test, special instructions and costs.
- Dynamic reformulation based upon ingredient characteristics, product weight, volume and cost.
- Perform formula “what if” physical, nutritional, and cost analysis, plus side-by-side version comparisons.
- Define multiple fill-levels and packaging sizes of the products with the same formula.
Costing
- Calculate expected finished good costs, including intermediates and assemblies, based upon the cost rollup of ingredients and packaging materials, as well as labor, setup and other production costs.
- Dynamically resize formulas to meet target costs.
- Perform ‘what-if’ cost scenarios.
- Compare costs for same formulas in different packaging configurations.
- Revaluate finished goods costs based on line item price-lists, special pricing and discount offers.
Traceability & Compliance
- Control formula access and maintain change history log.
- Track your products from receipt to shipment and vice-versa.
- Speed up lot recalls and audits.
- Design and print nutritional labels and supplemental information panels.
- Generate bi-directional lot traceability reports and specific product labelling and industry standard compliance reports.
- Design and produce lot recall letters.
- Support FDA, 21 CFR Part 11, GFSI and cGMP requirements.
Warehousing
- Manage receiving & putaway of raw materials, pick & issue raw materials into batch jobs, receive and store finished goods, pick & ship finished goods.
- Control the staging and issuing of raw materials into batch jobs.
- Integrate with weigh scales when issuing raw materials into equipment.
- Perform quality inspections and checklists.
- Execute tasks via paper documents (workstation data entry) or mobile devices (any html browser-based device).
Accounting
- Manage AR, AP, GL and invoicing.
- Streamline your financial operations by maintaining ledger, journal entries, tax calculations, multi-currency transactions and banking activities.
- Manage cash flow, track budgets, and compare actual versus plans to see where your business stands at a moment’s notice.
- Integration of financial operations in real-time with other business processes, for example purchasing and sales, to improve visibility into cash flow.
Sales
- Manage AR, AP, GL and invoicing.
- Single click transfer of quotes to order, and order to shipment.
- Volume-based scaled pricing, discounts, and mark-ups.
- Confirm and processes shipments, partial shipments, and back orders, and check inventory for parts’ availability.
- Define contracts & warranty, and generate sales reports, picklist, invoices, BOL, and COA.
Purchasing
- Create purchase requests, purchase orders, and define approvals.
- Maintain several price-list options to manage purchases, returns, and blanket agreements.
- Real-time dashboard to analyze & assess vendor, discounts, tax, contract, and other information.
- Support to supplier management, audit warnings, and purchase of cGMP material only from item-specific vendors.
- Achieve real-time synchronization of goods receipts and inventory warehouse levels.
CONTACT US / REQUEST A DEMO

Let’s see if BatchMaster Software has the right software solution for your needs. Contact Us to share something about your operations and software needs with our consultants or Request A Demo of one of our software applications.