Product Costing
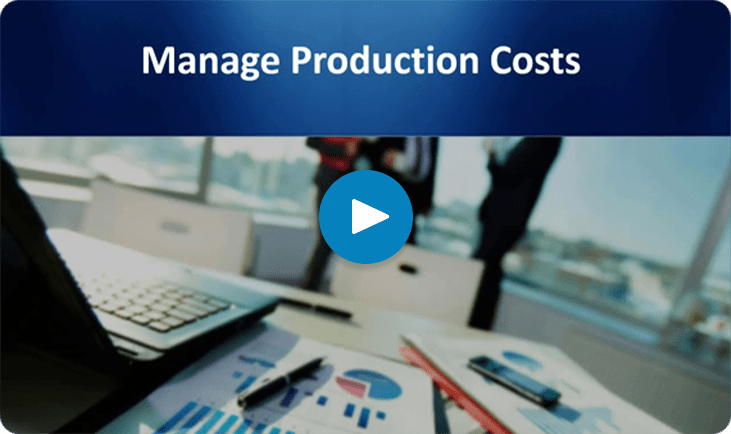
Ensure You Get The Highest Margin For Your Products
ENSURE YOU GET THE HIGHEST MARGIN FOR YOUR PRODUCTS

Costing capabilities are found throughout the production and distribution processes to ensure that your finished goods meet your corporate and customer’s expectations. Product development formulation and packaging bills of material take into account the costs of raw materials and consumables as well as projected costs associated to fixed setup charges, scalable labor, tiered labor, markups, margins and losses. Projected costs will be adjusted based upon the total batch size at time of production and any modifications of the batch job specifications. Further production costing analysis, such as actuals vs expected, can be performed by management using various dashboards and reports.
PROCESS MANUFACTURING FEATURES THAT WILL CHANGE THE WAY YOU WORK

With a tighter control over product and process costs from the time of product development
through batch production, you can reduce your bottom line.
through batch production, you can reduce your bottom line.
- Apply fixed, tiered and variable labor costs in formulation
- Add consumable costing in formulation
- Cost raw material based upon inventory evaluation methods in formulation
- Perform What If cost analysis in formulation
- Capture actual cost in production
- Analyze expected vs actual costs
CONTACT US / REQUEST A DEMO

Let’s see if BatchMaster Software has the right software solution for your needs. Contact Us to share something about your operations and software needs with our consultants or Request A Demo of one of our software applications.
DOCUMENTS

Costing
This data sheet provides a summary of pre and post production costing capabilities used by BatchMaster customers
VIDEOS

Comprehensive QC & QA
Nutra & Pharma processors – Discover the key software features you need to quickly move your concept from the laboratory into production, while ensuring label claims, tracking communications and managing multiple formula versions