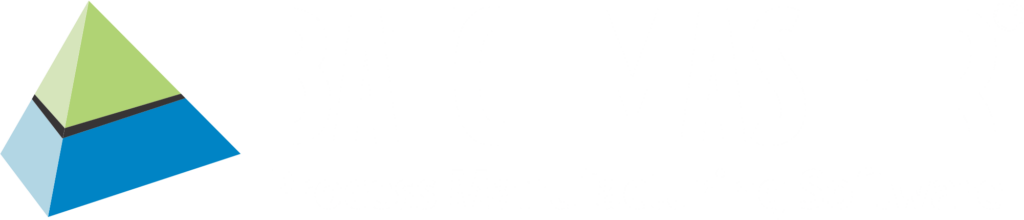
Process Manufacturing Software for Leading Financials
- Inventory management
- Traceability
- Quality control
- Production management
- Formulation
- Industry specific compliance
- Planning & Scheduling
Run Our Process Manufacturing Application with Your Current Financials

BatchMaster
Manufacturing
Application
Effectively Manage Your Plant Operations

Food Processing Software That Will Change the Way You Work

- Inventory
- Traceability
- Quality
- Production
- Formulation
- Compliance
- Planning & Scheduling
Inventory
Efficient inventory management ensures seamless tracking and movement of ingredients, packaging, and finished goods, while monitoring quality control statuses, weights, and plant locations.
Key features include:
- Attribute Management: Maintain records for allergens, safety, certifications, and industry-specific documents.
- Smart Allocation: Allocate inventory based on expiry dates and quality status.
- Batch Adjustments: Dynamically adjust batch jobs according to inventory characteristics.
- Mobile Warehousing: Execute warehousing tasks efficiently using mobile devices.
Traceability
Key features include:
- Automatic Lot Numbering: Assign lot numbers automatically during receiving and production.
- Lifecycle Tracking: Capture and validate lot numbers at every stage of production.
- Quick Searches: Perform bi-directional searches using an intuitive graphical tool.
- Recall Management: Generate barcoded labels (e.g., product labels, pallet licenses) to further streamline operations.
Quality
Integrate quality control and assurance throughout all processes, ensuring product safety and compliance.
Key features include:
- QC Testing: Set up quality control tests with specified tolerance and sample values.
- Inspection Plans: Execute comprehensive inspection plans and checklists.
- Documentation: Generate Certificates of Analysis (COA) and manage production deviations.
- Issue Management: Address customer complaints and nonconformance situations effectively.
Production
Optimize production processes for intermediates and finished goods, including co-products and by-products.
Key capabilities include:
- Dynamic Job Scheduling: Link and schedule dependent batch jobs based on resource availability.
- Resource Management: Manage equipment capacities and resource allocations efficiently.
- Deviation Capture: Record and address deviations during production runs.
- Inventory Backflushing: Automatically backflush inventory for completed jobs.
Formulation
Facilitate the management of product specifications across multiple versions and formulations.
Key features include:
- Dynamic Adjustments: Modify ingredient weights and volumes to achieve target properties.
- Cost Analysis: Account for fixed and variable labor and consumable costs.
- Specification Comparison: Analyze and compare different product specifications.
- Workflow Approval: Employ multi-level workflows for formulation approvals.
Compliance
Ensure adherence to federal and industry-specific regulations throughout every process.
Key functionalities include:
- Real-Time Alerts: Notify formulators when specifications exceed established levels.
- Data Capture: Mandate the collection of item, user, and location data for compliance (CFR 11).
- Audit Trail Maintenance: Maintain transactional history for auditor reporting, including Master Batch Records.
- Label Generation: Automatically generate required product and safety labels and documents.
Planning & Scheduling
Optimize production and procurement processes to meet demand effectively.
Key capabilities include:
- Comprehensive Planning: Establish short, medium, and long-range planning periods.
- Facility Management: Plan production by facility or across multiple locations.
- Supply and Demand Consolidation: Streamline supply and demand management across facilities.
- What-If Analysis: Perform scenario analysis while planning production schedules.
Inventory
Key features include:
- Automatic Lot Numbering: Assign lot numbers automatically during receiving and production.
- Lifecycle Tracking: Capture and validate lot numbers at every stage of production.
- Quick Searches: Perform bi-directional searches using an intuitive graphical tool.
- Recall Management: Generate barcoded labels (e.g., product labels, pallet licenses) to further streamline operations.
Quality
Key features include:
- QC Testing: Set up quality control tests with specified tolerance and sample values.
- Inspection Plans: Execute comprehensive inspection plans and checklists.
- Documentation: Generate Certificates of Analysis (COA) and manage production deviations.
- Issue Management: Address customer complaints and nonconformance situations effectively.
Production
Key capabilities include:
- Dynamic Job Scheduling: Link and schedule dependent batch jobs based on resource availability.
- Resource Management: Manage equipment capacities and resource allocations efficiently.
- Deviation Capture: Record and address deviations during production runs.
- Inventory Backflushing: Automatically backflush inventory for completed jobs.
Formulation
Key features include:
- Dynamic Adjustments: Modify ingredient weights and volumes to achieve target properties.
- Cost Analysis: Account for fixed and variable labor and consumable costs.
- Specification Comparison: Analyze and compare different product specifications.
- Workflow Approval: Employ multi-level workflows for formulation approvals.
Compliance
Key functionalities include:
- Real-Time Alerts: Notify formulators when specifications exceed established levels.
- Data Capture: Mandate the collection of item, user, and location data for compliance (CFR 11).
- Audit Trail Maintenance: Maintain transactional history for auditor reporting, including Master Batch Records.
- Label Generation: Automatically generate required product and safety labels and documents.
Planning & Scheduling
Optimize production and procurement processes to meet demand effectively.
Key capabilities include:
- Comprehensive Planning: Establish short, medium, and long-range planning periods.
- Facility Management: Plan production by facility or across multiple locations.
- Supply and Demand Consolidation: Streamline supply and demand management across facilities.
- What-If Analysis: Perform scenario analysis while planning production schedules.
Cloud Deployment Available

About Us

BatchMaster Software is a leading provider of Process Manufacturing ERP solutions that help companies worldwide meet their corporate objectives.
More than
2,000
Happy Customers
More than
2,500
Implementations
More than
40,000
Users
More than
30
Years of Experience
More than
500
Employees
More than
7
Offices
more than
40,000
Users
more than
30
Years of Experience